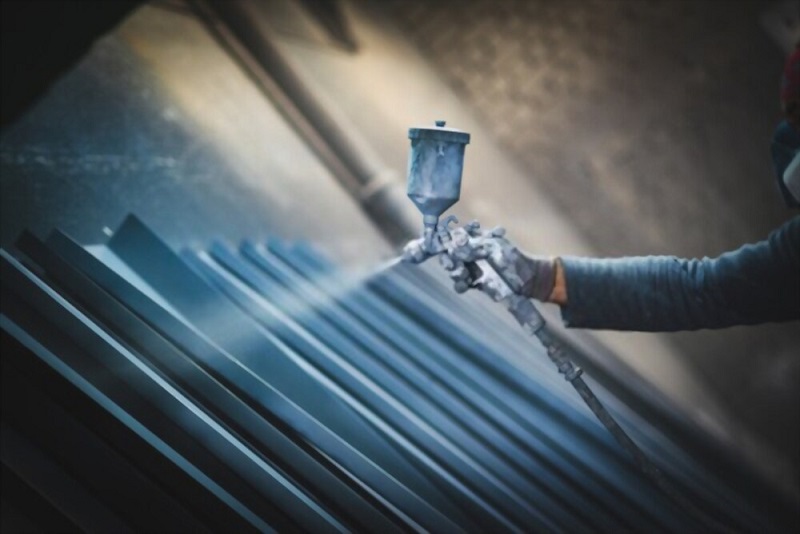
Since the introduction of steel, it has become one of the major used alloys of iron in various industries. Steel can’t corrode like iron, and it doesn’t even form rust so fast. However, that doesn’t mean steel will remain dust free for a lifetime. It does erode and form rust like iron but at a slower rate. Since these two are the greatest disadvantages of the materials, people now use galvanization to protect the quality and strength of both iron and steel.
 Galvanization Processing?
In galvanization, a layer of molten zinc is spread on the surfaces of an iron or a steel material. According to the metal activity series, zinc is placed first, followed by iron, the former is more reactive, which ensures that iron or steel can stay intact without taking part in any form of a chemical reaction. Galvanization is of two types- hot and cold galvanization.
What Is Cold Galvanization Paint?
Before learning about the cold galv paint, you need to know more about the process itself. In cold galvanization, the iron or steel structure is painted with a zinc-rich paint with a brush or sprays. These structures are not inserted into the molten zinc bath for a proper coating of the active metal.
In a cold galv paints, about ninety percent is powdered zinc is present, increasing the reactivity of the paint and protecting the core material, which is usually made of cast or wrought iron and steel. Along with the powdered zinc, organic binder material keeps the zinc molecules close to each other, thereby improving the coating’s resistivity and strength.
The paint is applied on the surface of the material on proper coatings in mind. The factors on which the zinc layer thickness will depend are:
- Condition of the steel or iron surface: if the material is recently polished and manufactured, the cold galv paint thickness will be average. Under such cases, the iron or steel material will require a lot of time to corrode or rust. However, if the surface condition is poorly damaged or average with signs of potential corrosion and rusting, the paint is applied in multiple layers to avoid further damages and protect the material.
- Composition of the steel: steel is an alloy of iron indeed. Apart from this, some other elements are also included, like carbon, silicon, chromium, and others. These elements ensure that the rate of corrosion and rusting can be slowed as compared to wrought or cast iron. So, depending on the composition of steel, the cold galv paint is applied with varying thickness.
What Are The Applications Of The Cold Galvanization Paint?
There are several areas where the zinc-rich galvanization paint is used. You need to learn more about these paints’ uses to ensure that you are correctly choosing the galvanization process for the iron or steel material.
- Small and fine materials can’t be dipped into the molten zinc bath protected with the cold galv paint.
- Thin steel or iron wires are also painted with zinc-rich paints because dipping them into the hot bath is not possible.
- If you want to apply a zinc coating on an already-constructed fixture such as railings or window grills, the best idea will be to use spray paint or brush paint.
- The cold galvanization paint is perfect for construction purposes where one needs to add an extra protective layer.
ConclusionÂ
In this article, we have discussed the basic things about the cold galv paint, which is now being widely used in several industries for keeping the iron or steel elements safe. Even though the paint doesn’t offer that much protection compared to the molten zinc coats, this galvanization process is cost-efficient and is the only option in certain cases.